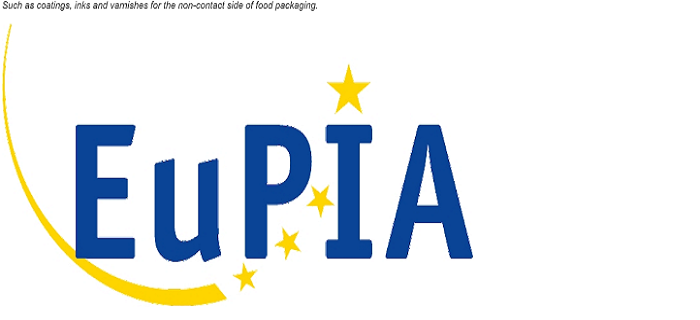
-
Ricardo Edward
- On February , 28 2020
- By Ricardo Edward
Doctor blade and uniform ink Metering
Doctor blade is an integral part of the printing process that provides the uniform metering. In order to achieve uniform metering, the correct doctor blade needs to be used for the job and it needs to be installed and set properly. This articles will provide details guidelines on how to achieve uniform metering throughout the run. There are many options in doctor blades and blade material you choose will have an effect on the metering quality and life of the blade. Typically metal carbon, stainless doctor blades will provide the best metering, followed by composites and then plastic blades. While the shape of the doctor blade tip rounded tip, lamella or either beveled edge also effect on the metering of ink.
Doctor blade angle adjustment in ink chamber also play a key role to control the ink metering during the printing process on machine. A generally acceptable flexo doctor blade contact angle range is 25 to 42 degrees, depending on the system. A doctor blade contact angle of 30 degrees is a nominal good angle for preventing print defects. If the doctor blade angle is less than 25 degrees then it will not provide the proper doctoring and require more force to doctor blade clearly and cause the dot gain and inconsistent print, possibly load dry ink or blade material into the cylinder and damage it. If the doctor blade contact angle is more than 42 degrees cause catching of the blade in the anilox cells resulting in lines across the web or vibration and other related print defects.
The next important factor that affect the ink metering in the flexographic printing is the doctor blade installation. If your doctor blade installation is not proper, doctor blade can’t meter the ink properly and cause the various print defect such as dirty print. Before the installation of the doctor blade, inspect the components and repair any damage found if possible. Minor things can usually be corrected by filing the damaged area smooth. When installing the doctor blade, be sure the back side of the blade is firmly resting on the ledge of pins that are built into the chamber in order to ensure that doctor blade is installed parallel to the chamber. Finally after the doctor blades are installed, look down the length of the blade to see if it is wrinkle free. During the installation also need to make sure that chamber is in alignment with the anilox roller or chamber centerlines are aligned with the anilox centerline and that it is not skewed to the anilox roll. Be sure that both blades touch the anilox roll at the same time and any misalignment between doctor blade and anilox roll will reduce the quality of the wipe that is delivered by the blade. Now question is arise how to check the alignment of chamber with anilox roll? The best way is to check the alignment with a plastic feeler gage that sliding between blade and anilox roll with slight tension and check the gap between rest of the blade and anilox roll that should be same everywhere on the blade and on the containment blade. If there is gap then adjust the chamber position as necessary until there is uniform gap on both blades. Be sure to follow any and all plant safety rules while checking the chamber alignment.
End seal also has the influence on the print defects as well as doctor blade ink metering and resulted into ink leakage from chamber instead of prevent the ink from flowing out of the chamber. On most presses with chamber and end seal, doctor blade also must be replaced and less pressure enhance the life of the end seal as well doctor blade, when setting for the printing. The performance of the end seal also based on the ink pump as well as flow rate. A greater flow rate of ink with the increase of machine speed add the pressure toward the end seal that cause leakage, slinging ink and waste substrate. Besides of all above, excessive application pressure is a significant cause of inconsistent blade metering due to deflecting of the doctor blade, flatten the doctor blade angle that prevent the uniform metering. Extreme pressures can deflect the blade to the extent that the blade tip will lift. This lifted blade tip can trap hard particles under with and lead to anilox scoring as well as critical print defects. So, uniform metering of ink by doctor blade ensure the defect less print, more customer retention and satisfaction.