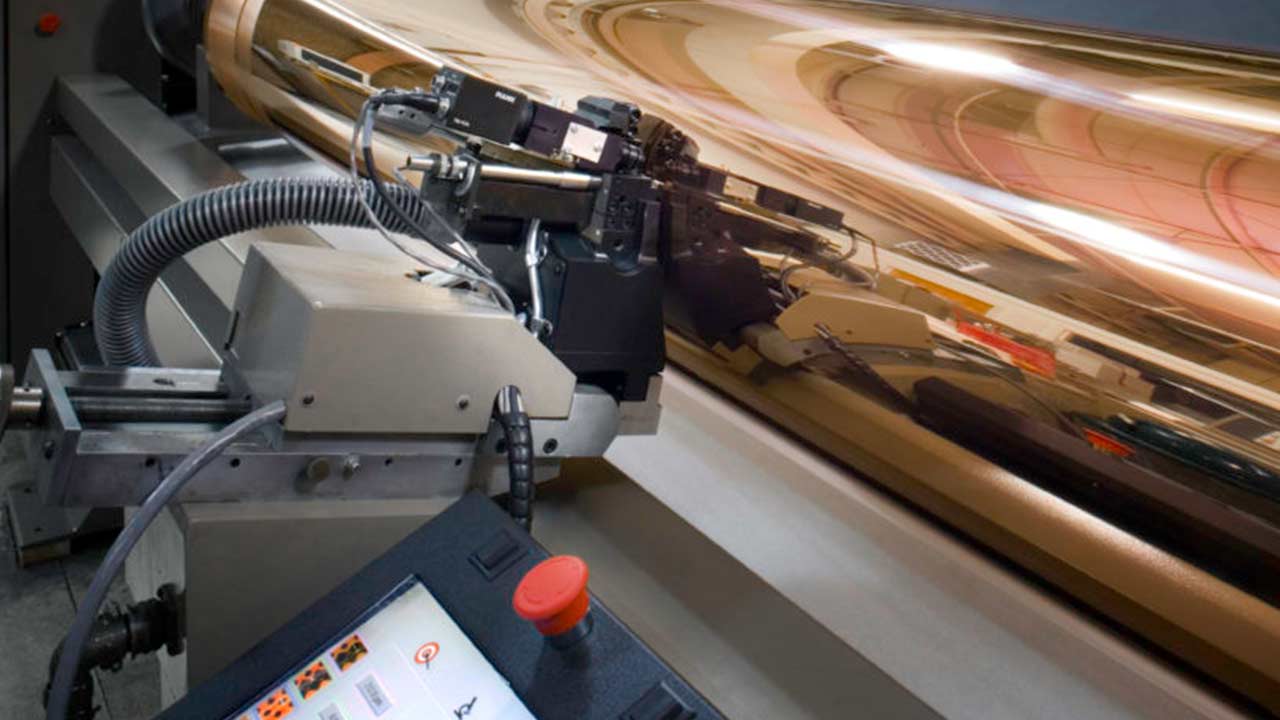
-
Faisal William
- On February , 28 2020
- By Faisal William
Introduction to Cylinder Engraving
Rotogravure is the premier, cost effective printing method for higher volume, high resolution packaging and displays. The principles of rotogravure printing underlines the fact that image areas are in a sunken area and the non-image areas are in relief that is why this is also known as intaglio printing. One of the most important feature of the gravure printing is the steel cylinder that is used as an image carrier. Gravure cylinders are usually made of steel and plated with the copper and then images are engraved on this cylinder by chemical etching or with a diamond tool and laser beam.
In general gravure cylinders are plated in chrome as a protective surface for the cells formed into the copper plated surface. These cells on the cylinder control the amount of the ink transfer on the substrate. In order to achieve more intensity of color on to the substrate deeper cells are required and smaller cells produces less ink density of color. The handling of chrome plating requires strict control, however so there has been a strong demand in the gravure cylinder making industry for a hard replacement material. The basic steps involve in the cylinder engraving are as follows;
- Removing the used gravure cylinders from the gravure printing press
- Washing the gravure cylinders to remove residual ink
- De-chroming or removing the chrome layer from steel cylinders
- Removing the copper image-carrying layer, either chemically, by means of electroplating, or mechanically
- Preparing the copper plating process (degreasing and deoxidizing, applying the barrier layer if the Ballard skin method was employed);
- Electroplating
- Surface finishing with a high-speed rotary diamond milling head and/or with a burnishing stone or a
- Polishing band
- Etching or engraving (producing the image on the gravure cylinder
- Test printing (proof print);
- Correcting the cylinder, minus or plus (i.e., reducing or increasing the volume of cells);
- Preparing the chrome-plating process (degreasing and deoxidizing, preheating, and – if necessary – sometimes polishing
- Chrome plating
- surface-finishing with a fine burnishing stone or abrasive paper
- Storing the finished cylinder or installing it directly in the gravure printing press.
The process control is very important during electromechanical engraving of gravure cylinders many problems arise like pin holes, stylus broken, shoe lines, cell depth variation, cell missing, thundering, centre out, pin holes, bludges, machine hang out. Patches, improper dots and depth variation and all these should be removed. The engraved cylinders has five major specification stylus, angle, that accuracy in also inevitable during the cylinder engraving and variation in these specification cause the various defects during the printing process. Engraved cylinder handling and storage is also very critical for the printer to maintain quality perfection and long lasting for optimum performance. The cylinder should be stored in racks to use for future jobs, automatically transported from one step to the next-from imaging to the press room and back to storage and during make ready, the press operator carefully loads the printing cylinders into the press.
By
Muhammad Sajid Khan